0 引言
大规模可再生能源的发展已成为全球能源消费向清洁化转型的重要趋势,目前中国的水电、风电、光伏发电的装机容量已达世界第一[1]。然而,受限于可再生能源发电的波动性,可再生能源消纳问题日益凸显[2]。2017年中国的弃水、弃风、弃光电量分别达到了515亿、419亿、73 亿kWh,总和已经超过了当年的三峡电站总发电量(976.05 亿kWh)[3]。
电转气技术(power to gas,P2G)是实现可再生能源规模化消纳的重要技术手段之一。通过以电解池为核心的电转气硬件系统,P2G可以将电能转化为氢气(H2)或甲烷(CH4)中的化学能,二者都是重要的气体燃料和工业原料,可以进入到后续的化工、交通、发电、供热、储气等丰富多样的终端应用中[4-6]。此外,P2G的负荷功率相对灵活[7-8],可以快速跟踪特定的功率调节指令,作为灵活负荷资源参与到电网调度中,从而改善电网灵活性,促进可再生能源消纳[9-10]。整个电转气环节是绿色环保的,主要原料是水,生成燃烧清洁的H2,几乎没有碳排放;或者在碳捕集而来的CO2参与下制取CH4,虽然CH4将来燃烧会排出CO2,但整个循环仍然是碳中性的。因此,可再生能源与电转气技术的整合是未来低碳化能源供给的美好愿景。
电解技术作为电能向化学能转化的核心环节,是P2G的核心技术。根据电解反应发生的温度范围,可以分为以碱性电解池(alkaline electrolysis cell,AEC)和质子交换膜电解池(proton exchange membrane electrolysis cell,PEMEC)为代表的低温电解技术,以及以固体氧化物电解池(solid oxide electrolysis cell,SOEC)为代表的高温电解技术[4,6,11]。其中,低温电解技术已经发展得相对成熟,进入应用推广阶段。目前,世界各地已有大量基于AEC和PEMEC的P2G示范项目落地[11],如位于德国Mainz的基于6 MW级PEMEC的电堆和8 MW风电场的Energiepark项目,其每小时氢气产量可达1000 m3 [8]。
高温电解技术在高温下直接对气态水进行电解,借助高温对电解反应在动力学和热力学方面的提升,显著降低电解电压,提高电解效率,并且具有高度可逆、可还原CO2等独特优势,成为近十几年电解技术的研究热点[4-5,12]。然而,高温的工作环境对材料、密封和装配工艺都提出了很高的要求,高温电解技术仍在研发试验阶段,成本较高,在大容量储能方面的应用还很少,目前较大容量的高温电解实验仍在千瓦级,如美国爱达荷国家实验室的15 kW高温电解实验平台[13]。高温电解技术的主要发展瓶颈在于高温下材料的高退化率,目前有大量研究尝试从稳定化处理、新型材料和次高温运行等角度解决这个问题[5]。
尽管技术上仍不够成熟,高温电解技术因其转化效率高等特有技术优势,仍然是大规模P2G储能方面最具潜力、最适合的技术路线。通过作为电—气—热多能耦合的大规模储能技术与电力系统结合,高温电解技术能够与未来的能源互联网有机融合,进一步提升区域能源利用效率。下文将从高温电解技术的工作原理、技术分类、转换模式、接入模式等方面,对高温电解储能技术进行更加细致的说明,详细论述高温电解技术在大规模电力储能方面的巨大应用潜力。
1 高温电解的工作原理
1.1 高温电解的反应原理
在特定的催化剂和直流电流的参与下,水分子(H2O)可以发生如公式(1)所示的化学反应,分解成氢气(H2)和氧气(O2)[5,14-15]

式中,∆H 为反应的摩尔焓变,其值表示每一摩尔该反应发生所需要吸收的能量。事实上,该能量可以进一步分为两部分[5]

一部分是吉布斯自由能变∆G ,这部分必须以电能形式提供;另一部分T∆ S以热量的形式吸收,可以来自外部热源,也可以来自额外电能产生的焦耳热。在进行电解时,H2O在阴极发生还原反应,从外电路得到电子,被分解成为H2和氧离子O2-。O2-则通过电解质传递到阳极,在阳极失去电子,发生氧化反应,生成O2,电子通过外电路的直流电源从阳极传递到阴极[5]。
电解水反应所需总能量∆H、电能∆G、热能T∆ S与温度的关系如图1所示[5,14],曲线根据查表所得的H2O、H2、O2热力学属性计算得到。显然,温度越高,以热能形式吸收的能量T∆ S就越多,反应所需的理论最低电能∆G 就越少。其本质原因在于反应是吸热反应,因而在热力学层面高温有利于该反应的正向进行。
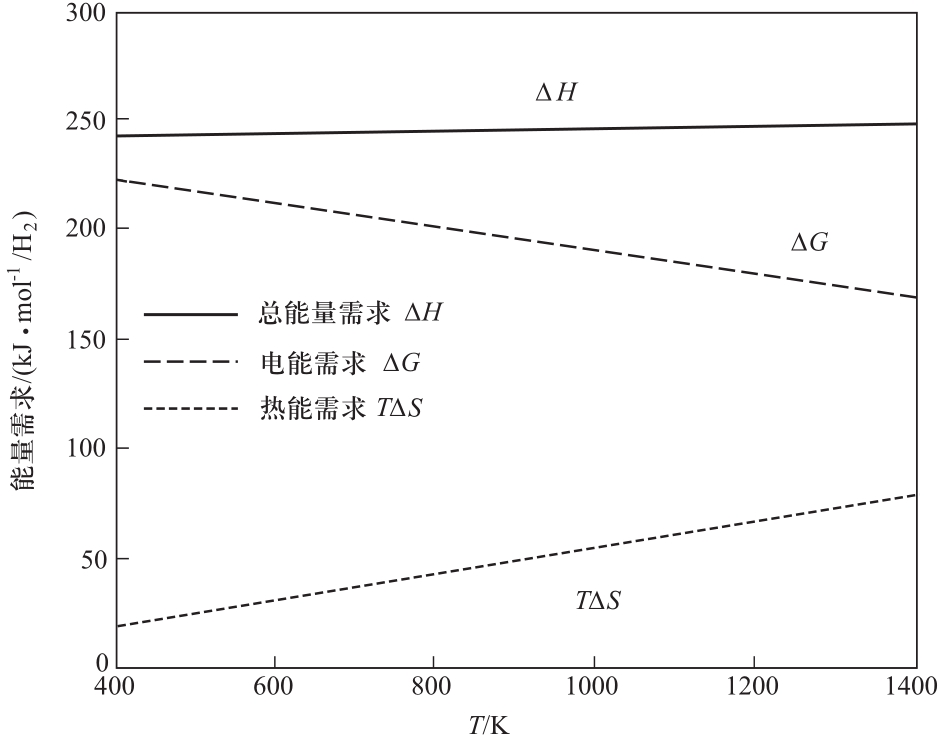
图1 电解反应所需总能量、电能、热能与温度的关系图
Fig.1 Temperature dependence of required total energy, electrical energy and thermal energy
实际计算电解所需电能时,除了要考虑提供吉布斯自由能变∆G 、使反应发生在热力学层面成为可能,还需要额外的电能来克服电解反应在动力学层面的阻力,记为∆E[14-15]。这部分额外电能∆E 往往用电解过电压表征,包含欧姆过电压、活化过电压、扩散过电压等对应不同阻力因素的过电压。事实上,由于高温对于化学动力学的提升,反应温度越高,电解过电压就越小,∆E 也越小。
根据以上定义,可求得电解池效率[5,14]

高温条件下,∆G、∆E 的值都要更小,反应同时在热力学层面和动力学层面得到提升,这就是高温电解池实现高效率电能转化的原理。
1.2 高温与低温电解的技术对比
根据1.1节所述,相较于低温电解,更高的电能转化效率是高温电解技术的首要优势。由于高温条件对电解反应的动力学和热力学提升明显,因而高温电解的系统效率比低温电解具有更大的提升潜力。
同时,高温电解池是高度可逆的。受益于高温电解的均相反应特性,高温电解池SOEC可以方便地切换到燃料电池工作模式,因而高温电解可以实现可逆运行[5,10,15];而低温电解池与低温燃料电池反应物的物相不同,因此需要采用不同的构造设计。
此外,高温电解具有碳耐受性。低温电解池的金属电极非常容易受到一氧化碳的毒化[5],即使是少量的碳杂质也会对电堆造成损坏;而高温电解池可以直接电解二氧化碳而不会被一氧化碳毒化,可以进行水—二氧化碳共电解制取氢气—一氧化碳,将氢气的甲烷化反应合并到电解池中,直接制取甲烷[5,11,16]。
最后,在多能源网络中,高温电解技术可参与高品位热量的梯级利用与多能源管理。高温电解需要制造高温反应环境,可与高温工业、供热管网结合形成热量的梯级利用,提升能源利用效率[17-18];同时高温电解也连接了电网与气网,有望通过多能源综合管理技术参与多网调控[19-20]。
高温电解、低温电解技术的详细特性对比如表1所示[4-5,21]。
表1 高温、低温电解技术的特性对比
Table 1 High-temperature electrolysis vs. low-temperature electrolysis
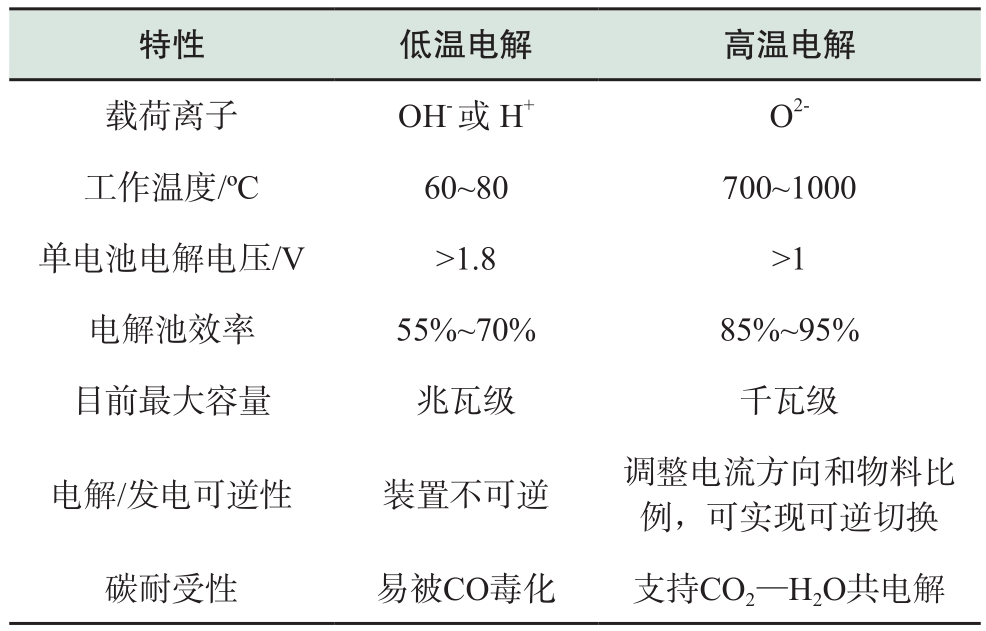
1.3 高温电解的主要技术障碍
高温工作条件在给电解池带来优良性能的同时,也为其大规模生产和应用增加了难度。事实上,由于常规材料和组件几乎都无法在高温电解所要求的700~1000 ºC下工作,基于陶瓷材料的高温电池电解质和电极研发一直以来是研究的热点,且至今没有适于大规模商业化生产的成熟技术[12,18];同时,高温为电池组堆过程中的电极贴合和气路密封带来了巨大的困难,适于高温的组堆和密封工艺同样是研发难点,制约了电堆容量,后文提到的板式电池尤为如此[13,21];更为重要的是,高温下主要工作材料的严重退化问题尚未得到经济有效的解决,很大程度上限制了高温电堆的工作寿命,影响了高温电解技术的经济性[5,21]。
由于上述因素的限制,目前高温电解技术仍在实验阶段,尚未被广泛实际应用。但是,一旦能够克服高温下的一系列材料和工艺问题,实现高温电解池的低成本生产,高温电解在大规模储能方面的应用投入指日可待。
2 高温电解电池的技术分类
根据几何结构划分,高温电解电池可以分为板式、管式以及扁管式3种[22-25]。尽管采用这3种技术的电池在外观上有较大差异,但是它们在组成部分以及工作原理上是相似的。其组成包括阳极、阴极、电解质、流道以及连接体五大部分,原理示意图见图2[26]。
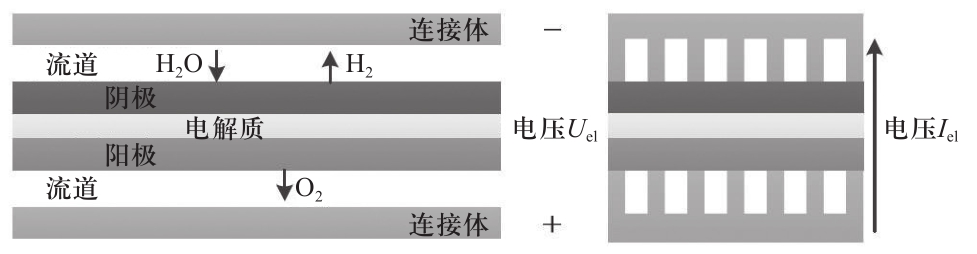
图2 高温电解电池的原理示意图
Fig.2 Schematic diagram of SOEC
在各组成部分中,流道起到传输气流的作用,反应物的水蒸气经过阴极流道,通入电池,而产物氢气以及氧气则分别经过阴极和阳极流道排出电池。阴极材料一般采用的是Ni/YSZ多孔金属陶瓷,阳极材料主要是多孔钙钛矿氧化物材料。多孔电极可以增加电极反应的有效面积。电解质为致密的氧化钇掺杂氧化锆陶瓷材料,能够隔绝阴极、阳极的气体,并在高温下传导氧离子。而连接体则是电导率较高的金属材料,起到集流的作用[26]。
通常情况下,单个电池的功率与电压较小,不能满足需求。因此在实际应用中,需要将多单个电池通过串并联形成电池堆,以达到更大的功率以及电压[22]。而采用不同技术的电池具有不同的几何外形,组成电池堆的方式不同,各自具有优势和劣势。以下介绍采用不同技术的电池的特点。
2.1 板式电池
板式电池的外观是一块平板,图3、图4分别是板式电池的结构以及板式电池堆的实物图[7,13]。
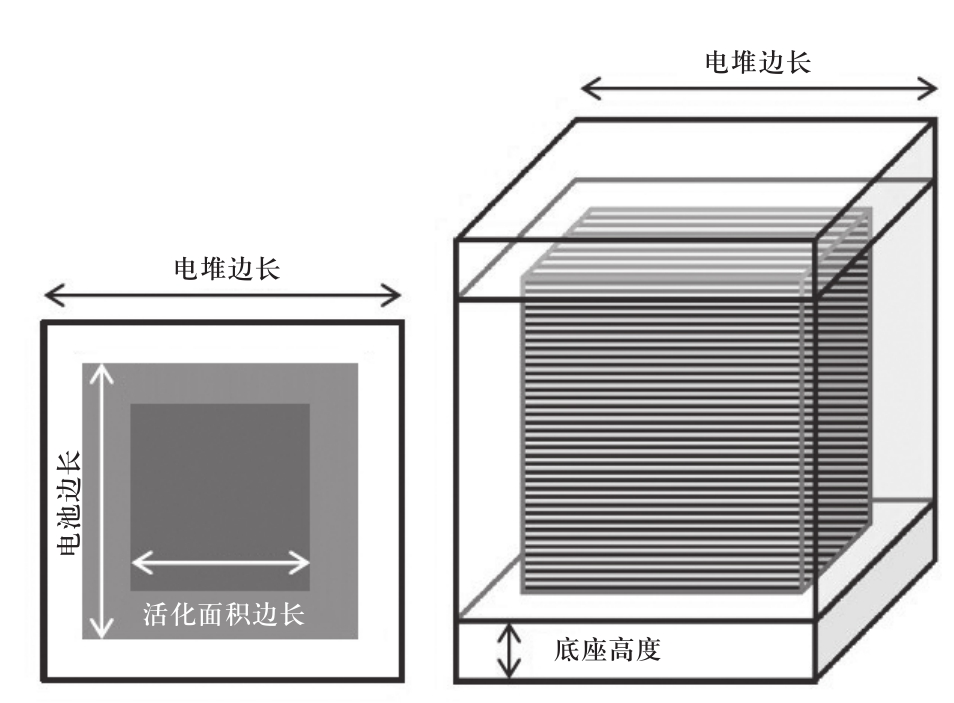
图3 板式电池和电堆结构图
Fig.3 SOEC scaling up to a stack
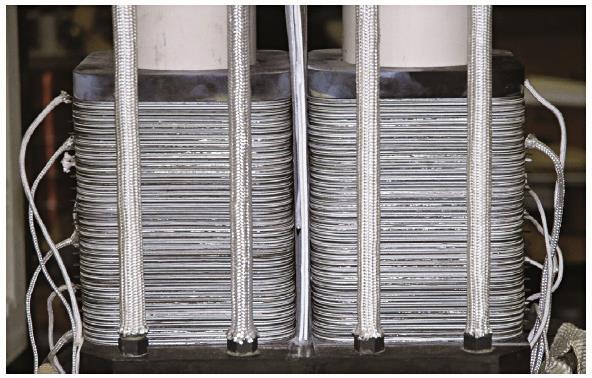
图4 板式电堆实物图
Fig.4 Picture of a planar SOEC stack
图3中的电池是由阴极、阳极、电解质3个部分堆叠形成的,其截面图如图2所示。而图4所示的电池堆则是由多个图3所示的电池与连接体堆叠形成的,实际上图2表示的就是电池堆中一个重复单元的截面图。
由于板式电池是平面结构,可以通过成熟的流延方法制造,工艺相对简单,制造成本较低。而且其电解质较薄、电流通过的面积大、结构紧凑,因此具有电阻低、功率密度大的优点。但由于板式电堆在运行时整体都处于高温环境中,所以密封困难是限制板式电池应用的一个因素。另外,由于电堆中的不同材料在高温下的热膨胀大小不同,因此容易产生较大的热应力,导致电堆寿命降低甚至损坏[22,24,27-28]。
2.2 管式电池
管式电池在结构上是一端封闭、一端开放的圆管,阴极、阳极分别位于管的内外壁,一种由西门子-西屋公司联合制造的管式电池的单电池以及电堆示意图如图5、图6[22]所示。
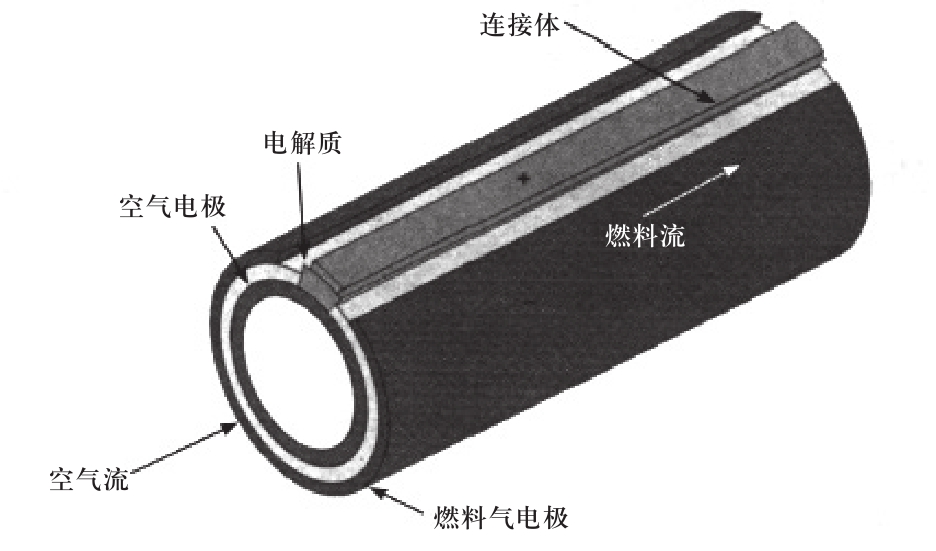
图5 西门子-西屋管式电池结构示意图
Fig.5 Schematic diagram of tubular SOEC made by Siemens-Westinghouse
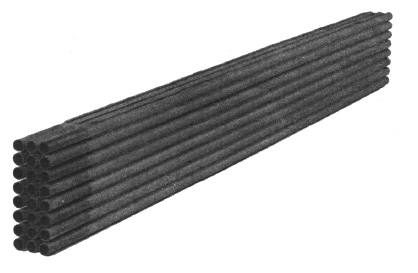
图6 西门子-西屋管式电堆示意图
Fig.6 Schematic diagram of tubular SOEC stack made by Siemens-Westinghouse
相比于板式电池,管式电池由于只有一端是开放的,而且在使用时,开放端的温度较低,因此在密封上更加容易。另外,管式电池与板式电池相比还具有更好的热应力耐受性,电池的稳定性更好,寿命更长[29]。但是,由于管式电池的外形是一个圆管,在工艺难度上比较大,制造成本高。另外,由于图6所示电堆中的单个电池可以长达数十厘米,制造工艺难以保证各圆管间的尺寸相同,因此也难以使各圆管之间良好接触,导致组堆难度高。图7为管式电堆的截面示意图[22],由图可见,若各圆管之间的尺寸不同,则无法使各电池间良好接触,不利于组堆。此外,由于管式电池中电流流经的路径较长,因此相比于板式电池,其电阻比较大[22,25,29]。
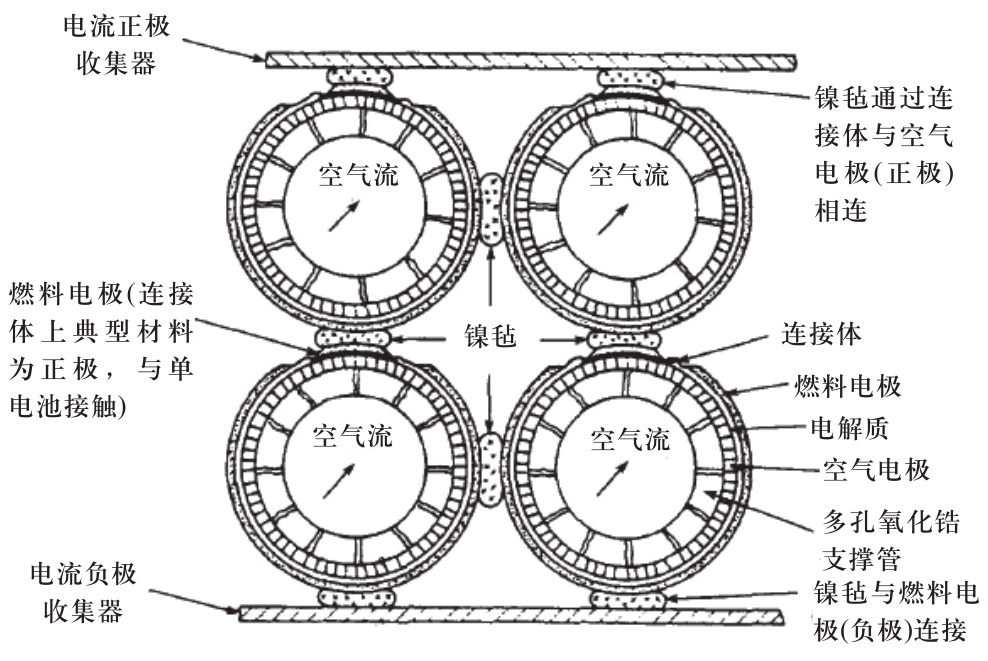
图7 西门子-西屋管式电堆截面示意图
Fig.7 Sectional view of tubular SOEC stack made by Siemens-Westinghouse
2.3 扁管式电池
为了在管式电池结构的基础上进一步提升功率密度,扁管式的结构设计应运而生。扁管式电池的出发点是将管式电池“压扁”以增大电池之间的接触面积,其横截面形状不是正圆形,而是长扁圆形,长扁的气道可以进一步划分为若干个气室,以增加上下两极之间的导电通路,如图8所示[25]。类似管式电池,扁管式电池工作时,每个气室都有物料气流通过,进行电解或发电,同时其开放端口温度较低、密封相对容易,热应力耐受性同样优于板式电池;并且,由于长扁外形和气道内分隔导体的设计,扁管式电池的内电阻和成堆电阻更小,可以实现更高的功率密度。总之,扁管式结构结合了板式结构集流面积大、电阻小,以及管式结构的容易密封、稳定性好、寿命长的优点,是极具潜力的新型高温电解池结构。扁管式电池组堆后的实物图如图9所示[23]。
虽然扁管式电池具有其他两种结构的优点,但是由于其出现时间较晚,因此扁管结构的相关研究不多,大部分从燃料电池的角度出发进行设计和实验,而且制造工艺也不成熟,还无法做到大规模生产[23,29,31-32]。
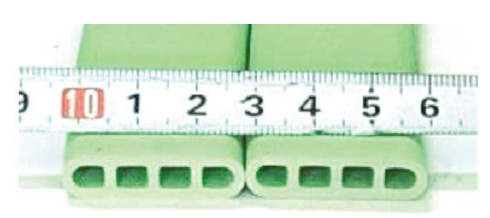
图8 扁管式电池实物图
Fig.8 Picture of flat-tubular SOEC
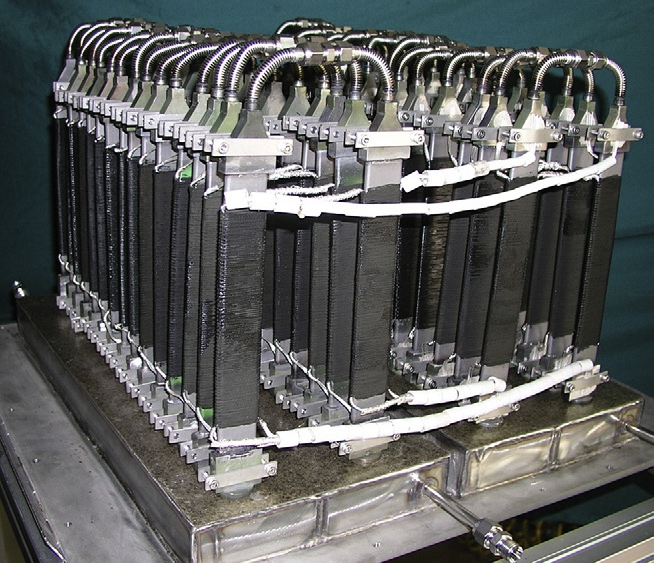
图9 扁管式电堆实物图
Fig.9 Picture of flat-tubular SOEC stack
3 高温电解系统的转换模式
3.1 H2O电解制氢
电解H2O制氢是目前高温电解技术的主要转换形式,其反应式如式(1)所示。
由1.1~1.2节可知,高温电解具有高电能转化效率,其电解池效率可达85%~95%,这一特性使得高温电解水制备氢气具有经济性上的潜力。然而,由于加热进料至电解池工作温度耗能高,且电解池出口气体余热未得到有效利用,在计入加热耗能后,单电池效率会下降约30%。
设计有效的外围辅助系统(balance of plant, BOP)对电解池进行热管理是提高系统效率的必要手段。实现热管理的核心元件为换热器,通过换热器设计,能够在系统中加入能量循环,回收利用出口气体余热。使用夹点分析设计换热网络或采用不同的换热器设计,可达到75%~83%的系统效率(LHV)[33-35]。一种外围辅助系统设计示意图如图10所示。
电解生成的氢气具有多种利用方式。如加压液化后通过储氢罐储存运输,作为化工原料参与后续化工合成反应,以及作为可燃性气体直接通入天然气管道等[33, 36-37]。
3.2 CO2电解制CO
除电解H2O外,高温电解技术还可直接电解CO2生成O2,反应过程如下
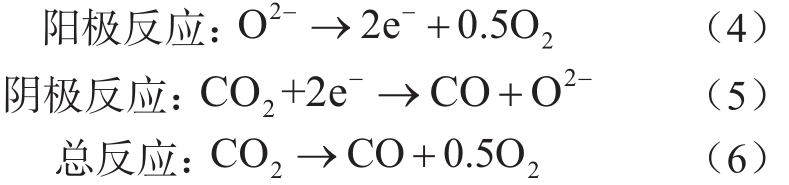
能够电解CO2是高温电解技术的独特优势。不过,与电解H2O相比,电解CO2单位面积电阻率(area specific resistance,ASR)更高[38],且可能发生布杜阿尔反应等副反应,产生积碳覆盖阴极活性位点,降低电解池性能和使用寿命[39]。通过控制流道中的CO/CO2比例,降低CO的体积分数,保证碳元素比例较低,可以显著降低积碳风险[39]。
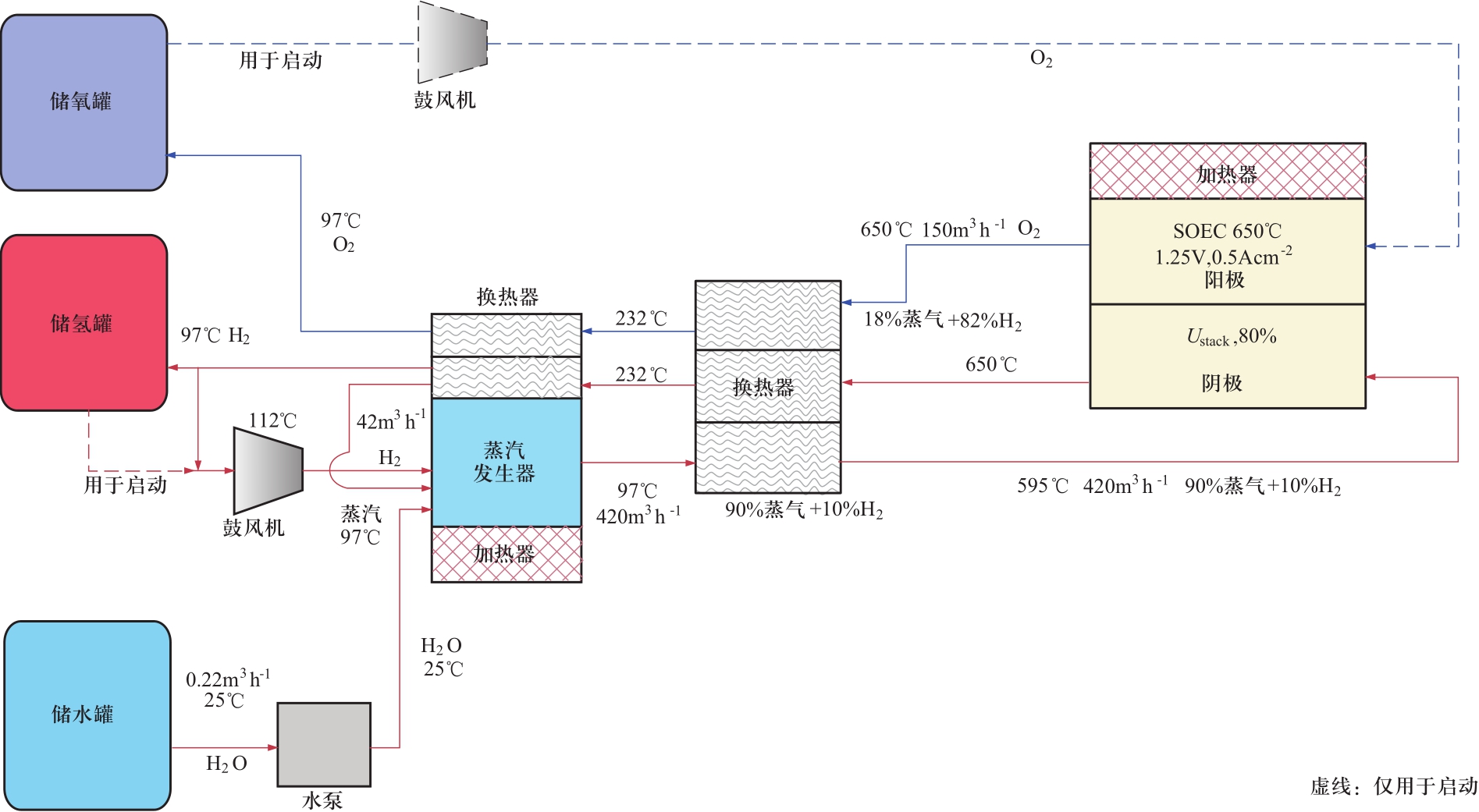
图10 一种外围辅助系统设计示意图
Fig.10 A BOP system design schematic
CO2电解可被应用于特定的场景下。如NASA利用火星大气的CO2环境,通过高温电解CO2制备O2供宇航员使用[39]。另外,在某些缺水地区,可利用电解生成的CO通过化工反应合成烃类燃料及甲醇等化工产物。
3.3 H2O+CO2共电解与化工合成
与单独电解H2O、CO2不同,H2O和CO2共电解时,除电解反应外,还会发生水煤气变换(water gas shift,WGS)反应,反应机理更复杂。

共电解时电解池的ASR与电解H2O时相近,大约是CO2电解的0.56倍[38],电解池性能有所提高。
另外,高温共电解通过电解H2O和CO2,直接生成高温CO2、CO、H2合成气,如图11所示[40]。大量化工合成反应如费托合成、甲烷化、甲醇化等,使用合成气作为原料,在较高温度压强下生成对应产物。高温共电解可作为化工合成的前一环节,在物质与能量两方面与后续流程耦合,从而提高系统整体效率。与分别电解H2O和CO2相比,共电解效率更高,且需要更少的电解步骤,降低了反应器成本。
由于化工合成反应的多样性,共电解与之结合后可生成多种产物,生成的产物应用广泛。如费托合成产物可用于合成汽油、煤油和柴油等发动机燃料,而甲醇、甲烷等产物既可作为清洁燃料,又可作为重要的化工原料[36,41-42]。
共电解与化工合成结合,将电能转化为化学能储存,是实现长时间大规模储能的有效手段。并且,由于其使用CO2作为原料生成有机物,可起到减少碳排放、生成可持续燃料的作用。
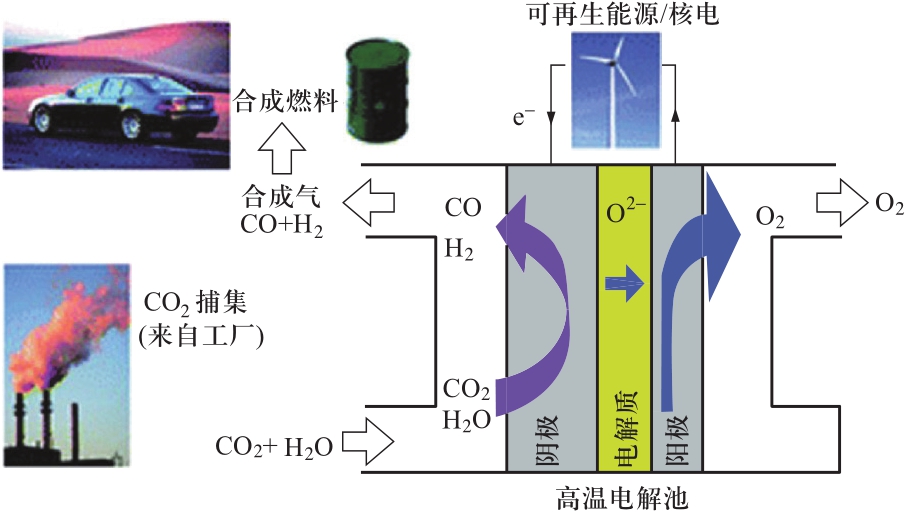
图11 SOEC共电解生成合成气示意图
Fig.11 Schematic diagram of CO2/H2O co-electrolysis using SOEC for syngas production
3.4 加压电解内合成
高温共电解在加压条件下,电解池内部存在甲烷内合成反应,可直接生成产物甲烷。

常规电解制甲烷流程将电解池与甲烷化反应器连接,电解产物H2通入甲烷化反应器内,与CO2反应生成甲烷,其电—气转换效率约为81.08%[43]。
对于加压电解内合成,通过将电解反应与甲烷化反应集成在电解池内,电解反应吸收甲烷化释放出的热量,实现了系统中热能的有效利用。与常规电解制甲烷相比,加压电解内合成流程简单且效率高,有望实现94.5%的电—气转换效率[44]。
4 高温电解系统的接入模式
4.1 纯电电解接入新能源电力系统
纯电电解指使用电能为系统辅机及电解供能,将进料从常温加热至高温电解池工作温度,并完成后续电解及产物加压储存等流程。
使用纯电电解的接入方式时,高温电解池在电力系统中作为电负荷,将电能转化为化学能储存,在新能源波动导致电能富余时起到消纳弃电的作用[43,45]。
由于高温电解出口气体温度高,因此可将高温电解系统与热网结合,使用电解产物作为热能载体,供热降温后再对电解产物加以利用。这种“气—热联供”的形式不仅提升了高温电解系统余热利用的能力,而且以高温电解系统作为能量接口,实现了电—气—热多能源网络的连接。
4.2 余热辅助电解接入“电—热”多能系统
对于高温电解系统,由于高温电解反应自身的吸热特性以及加热进料至电解温度的需求,热能在系统所需总供能中占有一定比例。4.1节提到的采用纯电供能的方式,将一部分高品位的电能转化为低品位热能,这种低效率的能量利用方式会导致额外的㶲损失。
使用外部热源替代电供热是提高高温电解系统制氢效率的有效方式,高温电解系统效率随外加热源温度变化如图12所示[46]。高温电解系统与核反应堆联合运行可实现系统52.6%的产氢热效率[47],火电机组[48]、太阳能光热反应器[49]等均可以作为外部热源,通过相对廉价的热能形式为高温电解供热,提升系统产氢热效率与经济效益。
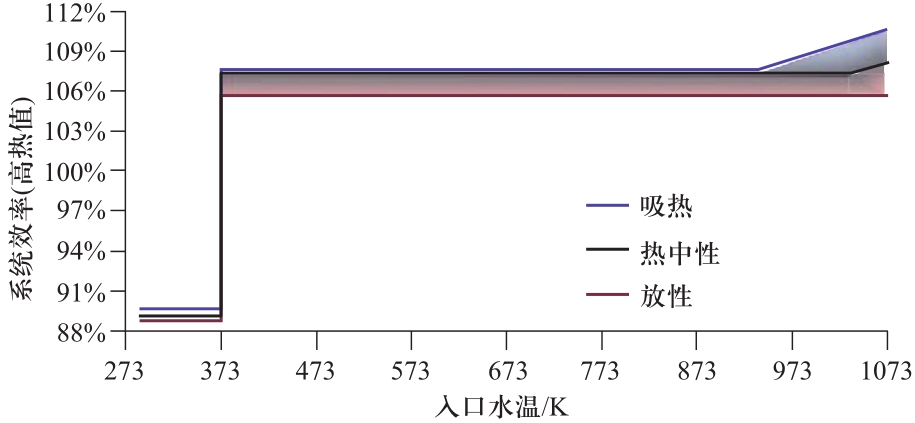
图12 高温电解系统效率随外加热源温度变化图
Fig.12 High-temperature electrolysis system efficiency changes with external heating source temperature
另外,热电联产机组(combined heat and power,CHP)由于已经具备抽汽供热能力,无需额外进行设备改造,便可与高温电解系统连接。在CHP热负荷不足时,供热抽汽有所富余,使用200~300 ℃抽汽为高温电解系统供热,可以提升高温电解系统的㶲效率与储能效率。
高温电解系统采用CHP作为外部热源时,其同时作为CHP的热负荷以及电力系统的电负荷,将剩余电、热以化学能的形式储存,在“电—热”多能系统中实现高效储能。
4.3 加压可逆规模化高效储气发电
根据1.2节中所述,高温电解池具有高度可逆的性质,可在电解、发电模式下自由转换。因此,其除了可在纯电电解和余热辅助电解模式下作为电、热负荷,还可作为电源发电上网,实现可逆储能的功能。
加压可以提升高温电解系统储能时的电—气—电循环效率。当加压高温电解系统运行在电解池模式时,由3.4节可知,会发生甲烷内合成反应。内合成反应放热供电解使用,可减少电解池内净吸热量。当系统以甲烷为进料,运行在燃料电池模式时,电池内存在吸热的内重整反应。甲烷氧化反应的放热量供内重整反应使用,减少了燃料电池内的净放热量。由于在电—气转换过程中输入的电能以及在气—电转换过程中损失的热能均减少,因此系统电—气—电效率得以提升[50]。

通过加压高温电解系统可逆运行的方式,有望实现80%的电—气—电循环效率[45],其放电时间可长达1000 h,储能成本约为3美分/kWh,具有高效率、长时间、低成本的特点[51]。
常见的储能技术最大放电时间、储能成本、循环效率如图13所示[51]。可见使用可逆固体氧化物电池(reversible solid oxide cell, ReSOC)储能与其他储能方式相比,具有特定的应用场景,在成本上有竞争力。
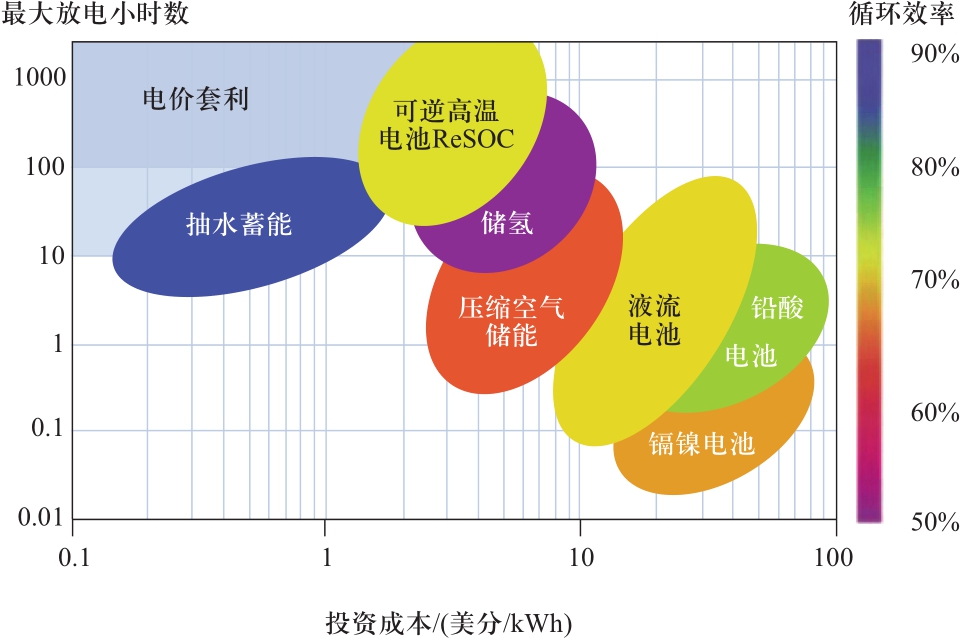
图13 储能技术对比图
Fig.13 Energy storage technology comparison chart
5 总结与展望
得益于高温条件对电解反应的热力学与动力学提升,高温电解在转化效率、可逆工作、碳耐受等方面显著优于常温电解。在实现结构上,新兴的扁管式结构兼具了板式与管式的结构优点;在转换模式上,高温电解池可单独制取H2或CO,也可共电解直接合成CH4;在系统接入模式上,纯电电解接入、余热辅助电解接入、可逆的储气发电接入等多种模式,能够在高效消纳可再生能源的同时提供丰富的灵活性资源。随着高温电解材料与工艺研发的不断深入,配合以面向富余电量的新型购电模式和氢燃料电池汽车等终端需求的发展,高温电解在大规模储能方面的应用指日可待,将对全球能源互联网的运行形态产生长足的影响。
参考文献
[1]Buckley T, Nicholas S, Brown M. China 2017 review: World’s Second-biggest Economy Continues to Drive Global Trends in Energy Investment[R]. Institute for Energy Economics and Financial Analysis, Cleveland: OH, Jan. 2018.
[2]白建华,辛颂旭,刘俊,等. 中国实现高比例可再生能源发展路径研究[J]. 中国电机工程学报,2015,35(14):3699-3705.Bai Jianhua, Xin Songxu, Liu Jun, et al. Roadmap of Realizing the High Penetration Renewable Energy in China[J]. Proceedings of the CSEE, 2015, 35(14): 3699-3705(in Chinese).
[3]姚金楠. 去年可再生能源弃电量超1000亿度[N/OL]. 中国能源报,2018: 2 (2018-1-29) [2018-5-10]. http://paper.people.com.cn/zgnyb/ html/2018-01/29/content_1833775.htm.
[4]Schiebahn S, Grube T, Robinius M, et al. Power to gas:Technological Overview, Systems Analysis and Economic Assessment for a Case Study in Germany[J]. International Journal of Hydrogen Energy, 2015, 40(12): 4285-4294.
[5]Lehner M, Tichler R, Steinmüller H, et al. Power-to-Gas:Technology and Business Models[M]. New York: Springer, 2014.
[6]Qadrdan M, Abeysekera M, Chaudry M, et al. Role of Powerto-Gas in an Integrated Gas and Electricity System in Great Britain[J]. International Journal of Hydrogen Energy, 2015,40(17): 5763-5775.
[7]Petipas F, Brisse A, Bouallou C. Model-Based Behaviour of a High Temperature Electrolyser System Operated at Various Loads[J]. Journal of Power Sources, 2013, 239: 584-595.
[8]Kopp M, Coleman D, Stiller C, et al. Energiepark Mainz:Technical and Economic Analysis of the Worldwide Largest Power-to-Gas Plant with PEM Electrolysis[J]. International Journal of Hydrogen Energy, 2017, 42(19): 13311-13320.
[9]Khani H, Farag H E Z. Optimal Day-Ahead Scheduling of Power-to-Gas Energy Storage and Gas Load Management in Wholesale Electricity and Gas Markets[J]. IEEE Transactions on Sustainable Energy, 2018, 9(2): 940-951.
[10]Frank M, Deja R, Peters R, et al. Bypassing Renewable Variability with a Reversible Solid Oxide Cell Plant[J].Applied Energy, 2018, 217: 101-112.
[11]Gahleitner G. Hydrogen from Renewable Electricity: An International Review of Power-to-Gas Pilot Plants for Stationary Applications[J]. International Journal of Hydrogen Energy, 2013, 38(5): 2039-2061.
[12]Li Q, Zheng Y, Guan W, et al. Achieving High-Efficiency Hydrogen Production Using Planar Solid-Oxide Electrolysis Stacks[J]. International Journal of Hydrogen Energy, 2014,39(21): 10833-10842.
[13]Zhang X, O’Brien J E, Tao G, et al. Experimental Design,Operation, and Results of a 4 kW High Temperature Steam Electrolysis Experiment[J]. Journal of Power Sources, 2015,297: 90-97.
[14]Udagawa J, Aguiar P, Brandon N P. Hydrogen Production through Steam Electrolysis: Model-Based Steady State Performance of a Cathode-Supported Intermediate Temperature Solid Oxide Electrolysis Cell[J]. Journal of Power Sources,2007, 166(1): 127-136.
[15]Kazempoor P, Braun R J. Model Validation and Performance Analysis of Regenerative Solid Oxide Cells for Energy Storage Applications: Reversible Operation[J]. International Journal of Hydrogen Energy, 2014, 39(11): 5955-5971.
[16]Li Q, He R, Gao J A, et al. The CO Poisoning Effect in PEMFCs Operational at Temperatures up to 200 C[J]. Journal of the Electrochemical Society, 2003, 150(12): A1599-A1605.
[17]O’Brien J E, McKellar M G, Harvego E A, et al. High-Temperature Electrolysis for Large-Scale Hydrogen and Syngas Production from Nuclear Energy–Summary of System Simulation and Economic Analyses[J]. International Journal of Hydrogen Energy, 2010, 35(10): 4808-4819.
[18]Ishihara T, Kanno T. Steam Electrolysis Using LaGaO3 Based Perovskite Electrolyte for Recovery of Unused Heat Energy[J].ISIJ International, 2010, 50(9): 1291-1295.
[19]李杨,刘伟佳,赵俊华,等. 含电转气的电—气—热系统协同调度与消纳风电效益分析[J]. 电网技术,2016,40(12):3680-3688.Li Yang, Liu Weijia, Zhao Junhua, et al. Optimal Dispatch of Combined Electricity-Gas-Heat Energy Systems with Power-to-Gas Devices and Benefit Analysis of Wind Power Accommodation[J]. Power System Technology, 2016, 40(12):3680-3688(in Chinese).
[20]Clegg S, Mancarella P. Integrated Electrical and Gas Network Flexibility Assessment in Low-Carbon Multi-Energy Systems[J]. IEEE Transactions on Sustainable Energy, 2016,7(2): 718-731.
[21]Mathiesen B V, Ridjan I, Connolly D, et al. Technology Data for High Temperature Solid Oxide Electrolyser Cells,Alkali and PEM Electrolysers[J]. Denmark: Department of Development and Planning, Aalborg University, 2013.
[22]Subhash C.Singhal, Kevin Kendall. 高温固体氧化物燃料电池: 原理、设计和应用[M]. 北京:科学出版社, 2007.
[23]Lim T H, Park J L, Lee S B, et al. Fabrication and Operation of a 1kW Class Anode-Supported Flat Tubular SOFC Stack[J]. International Journal of Hydrogen Energy, 2010, 35(18): 9687-9692.
[24]Luo Y, Shi Y, Li W, et al. Comprehensive Modeling of Tubular Solid Oxide Electrolysis Cell for Co-Electrolysis of Steam and Carbon Dioxide[J]. Energy, 2014, 70(3): 420-434.
[25]Kim J H, Song R H, Song K S, et al. Fabrication and Characteristics of Anode-Supported Flat-Tube Solid Oxide Fuel Cell[J]. Journal of Power Sources, 2003, 122(2): 138-143.
[26]牟树君,林今,邢学韬,等. 高温固体氧化物电解水制氢储能技术及应用展望[J]. 电网技术,2017,41(10):3385-3391.Mu Shujun, Lin Jin, Xing Xuetao, et al. Technology and Application Prospect of High-Temperature Solid Oxide Electrolysis Cell[J]. Power System Technology, 2017, 41(10):3385-3391(in Chinese).
[27]Park J, Kang J, Bae J. Computational Analysis of Operating Temperature, Hydrogen Flow Rate and Anode Thickness in Anode-Supported Flat-Tube Solid Oxide Fuel Cells[J].Renewable Energy, 2013, 54(6): 63-69.
[28]Lin B, Shi Y, Meng N, et al. Numerical Investigation on Impacts on Fuel Velocity Distribution Nonuniformity Among Solid Oxide Fuel Cell Unit Channels[J]. International Journal of Hydrogen Energy, 2015, 40(7): 3035-3047.
[29]Park J, Bae J, Kim J Y. A Numerical Study on Anode Thickness and Channel Diameter of Anode-Supported Flat-Tube Solid Oxide Fuel Cells[J]. Renewable Energy, 2012,42(1): 180-185.
[30]Park J, Bae J, Kim J Y. The Current Density and Temperature Distributions of Anode-Supported Flat-Tube Solid Oxide Fuel Cells Affected by Various Channel Designs[J]. International Journal of Hydrogen Energy, 2011, 36(16): 9936-9944.
[31]Suzuki T, Liang B, Yamaguchi T, et al. Development of Novel Micro Flat-Tube Solid-Oxide Fuel Cells[J]. Electrochemistry Communications, 2011, 13(7): 719-722.
[32]Suzuki T, Yamaguchi T, Sumi H, et al. Evaluation of Micro Flat-Tube Solid-Oxide Fuel Cell Modules Using Simple Gas Heating Apparatus[J]. Journal of Power Sources, 2014, 272:730-734.
[33]Petipas F, Brisse A, Bouallou C. Benefits of External Heat Sources for High Temperature Electrolyser Systems[J]. International Journal of Hydrogen Energy, 2014, 39(11): 5505-5513.
[34]Meng N, Leung M K H, Leung D Y C. Energy and Exergy Analysis of Hydrogen Production by Solid Oxide Steam Electrolyzer Plant[J]. International Journal of Hydrogen Energy, 2007, 32(18): 4648-4660.
[35]Wang Z, Mori M, Araki T. Steam Electrolysis Performance of Intermediate-Temperature Solid Oxide Electrolysis Cell and Efficiency of Hydrogen Production System at 300Nm3h-1[J].International Journal of Hydrogen Energy, 2010, 35(10): 4451-4458.
[36]Giglio E, Lanzini A, Santarelli M, et al. Synthetic Natural Gas via Integrated High-Temperature Electrolysis and Methanation:Part I—Energy Performance[J]. Journal of Energy Storage,2015, 1(12): 22-37.
[37]黄明,吴勇,文习之,等. 利用天然气管道掺混输送氢气的可行性分析[J]. 煤气与热力,2013,33(4):39-42.Huang Ming, Wu Yong, Wen Xizhi, et al. Feasibility Analysis of Hydrogen Transport in Natural Gas Pipeline[J]. Gas & Heat,2013, 33(4): 39-42(in Chinese).
[38]Zheng Y, Wang J, Yu B, et al. A Review of High Temperature Co-Electrolysis of H2O and CO2to Produce Sustainable Fuels Using Solid Oxide Electrolysis Cells (SOECs): Advanced Materials and Technology[J]. Chemical Society Reviews,2017, 46(5): 1427-1463.
[39]Shi Y, Luo Y, Cai N, et al. Experimental Characterization and Modeling of the Electrochemical Reduction of CO2in Solid Oxide Electrolysis Cells[J]. Electrochimica Acta, 2013, 88(2):644-653.
[40]Fu Q, Mabilat C, Zahid M, et al. Syngas Production via High-Temperature Steam/CO2Co-Electrolysis: An Economic Assessment[J]. Energy & Environmental Science, 2010, 3(10):1382-1397.
[41]Becker W L, Braun R J, Penev M, et al. Production of Fischer–Tropsch Liquid Fuels from High Temperature Solid Oxide Co-Electrolysis Units[J]. Energy, 2012, 47(1): 99-115.
[42]Al-Kalbani H, Xuan J, García S, et al. Comparative Energetic Assessment of Methanol Production from CO2: Chemical Versus Electrochemical Process[J]. Applied Energy, 2016,165: 1-13.
[43]Stempien J P, Ni M, Sun Q, et al. Production of Sustainable Methane from Renewable Energy and Captured Carbon Dioxide with the Use of Solid Oxide Electrolyzer: Athermodynamic Assessment[J]. Energy, 2015, 82: 714-721.
[44]Luo Y, Shi Y, Li W, et al. Synchronous Enhancement of H2O/CO2, Co-Electrolysis and Methanation for Efficient One-Step Power-to-Methane[J]. Energy Conversion & Management,2018, 165: 127-136.
[45]Wendel C H, Gao Z, Barnett S A, et al. Modeling and Experimental Performance of an Intermediate Temperature Reversible Solid Oxide Cell for High-Efficiency, Distributed-Scale Electrical Energy Storage[J]. Journal of Power Sources,2015, 283: 329-342.
[46]Petipas F, Brisse A, Bouallou C. Benefits of External Heat Sources for High Temperature Electrolyser Systems[J]. International Journal of Hydrogen Energy, 2014, 39(11): 5505-5513.
[47]O’Brien J E, Mckellar M G, Harvego E A, et al. High-Temperature Electrolysis for Large-Scale Hydrogen and Syngas Production from Nuclear Energy – Summary of System Simulation and Economic Analyses[J]. International Journal of Hydrogen Energy, 2010, 35(10): 4808-4819.
[48]Manage M N, Sorensen E, Simons S, et al. A Modelling Approach to Assessing the Feasibility of the Integration of Power Stations with Steam Electrolysers[J]. Chemical Engineering Research & Design, 2014, 92(10): 1988-2005.
[49]Balta M T, Kizilkan O, Yılmaz F. Energy and Exergy Analyses of Integrated Hydrogen Production System Using High Temperature Steam Electrolysis[J]. International Journal of Hydrogen Energy, 2016, 41(19): 8032-8041.
[50]Bierschenk D M, Wilson J R, Barnett S A. High Efficiency Electrical Energy Storage Using a Methane–Oxygen Solid Oxide Cell[J]. Energy & Environmental Science, 2011, 4(3):944-951.
[51]Jensen S H, Graves C, Mogensen M, et al. Large-Scale Electricity Storage Utilizing Reversible Solid Oxide Cells Combined with Underground Storage of CO2and CH4[J].Energy & Environmental Science, 2015, 8(8): 2471-2479.
Large Scale Energy Storage Technology Based on High-Temperature Electrolysis
XING Xue-tao1, LIN Jin1, SONG Yong-hua1,2, QI Ruo-mei1, CHI Ying-tian1, WU Jian3, ZHOU You4, MU Shu-jun4
(1. Department of Electrical Engineering, Tsinghua University, Haidian District, Beijing 100084, China;2. Department of Electrical and Computer Engineering, University of Macau, Macau, China;3. Zhejiang Zhentai Energy Tech. Co., Ltd., Lishui 321400, Zhejiang Province, China;4. National Institute of Clean and Low Carbon Energy, Changping District, Beijing 102211, China)
Abstract:Power-to-gas (P2G) presents a charming solution for the efficient utilization of massive surplus electricity production. The core technology for P2G can be further divided into two types by the operating temperature: low-temperature electrolysis and high-temperature electrolysis. Usually based on solid oxide electrolysis cells, the high-temperature electrolysis has advantages of high conversion efficiency, various (carbontolerant) products and reversible abilities. This paper presents a detailed introduction of the technical characteristics of hightemperature electrolysis and its potential applications in energy storage. Specifically, the following contents are included: the working principle and technical obstacles of high-temperature electrolysis and its primary differences with low-temperature electrolysis, the primary types and characteristic comparisons of high-temperature electrolysis cells, and several different material transformation modes and system operations of hightemperature electrolysis, and in the end, some possible manners and benefits of its application in the future energy internet.
Keywords:large scale energy storage; power-to-gas; hightemperature electrolysis; solid oxide electrolysis cell
Project Supported by National Natural Science Foundation of China (51577096, 51761135015), Project Supported by National Key Research and Development Program of China International S&T Cooperation (2016YFE0102600).
邢学韬
作者简介:
邢学韬(1992),男,博士研究生,主要从事电转气系统的优化运行、电转气参与可再生能源消纳等相关技术研究工作。E-mail: xxt15@mails.tsinghua.edu.cn。
林今(1985),男,博士,副教授,主要从事新能源电力系统的运行控制、氢能的接入与控制、能源物联网等相关技术研究工作。E-mail: linjin@tsinghua.edu.cn。
宋永华(1964),男,博士,教授,英国皇家工程院院士,主要从事智能电网、电力市场、多能源系统等相关技术研究工作。
(责任编辑 赵杨)